Here’s how wearable sensors make the workplace more safe
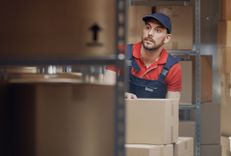
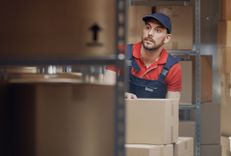
April 28th is observed internationally as the day for safety and health at work. To mark this relatively unknown albeit important day, we thought we would publish an in-depth case study on the ways in which IoT technology is being deployed towards making the workplace safer and reducing work-related injuries and deaths. In this post, we have highlighted the ways in which IoT technology and wireless sensors are being used to ensure higher levels of workplace safety and the various capacities in which they are being used.
A study conducted by the International Labour Organisation found that each year, work-related accidents account for over 370 million injuries and over 2.7 million deaths. The same study claims that, on average, businesses and corporations spend about 3.94% of global GDP on employee treatment - it is estimated that workplace injuries cost American companies a whopping $62 billion per year.
So, it’s pretty clear. Workplace accidents are expensive, both in terms of avoidable human suffering and in terms of productivity and economic losses. Granted, there will always be a certain amount of risk inherent in performing actions in the world. A lot of these risks are accounted for when salaries are negotiated and agreements are signed.
Nevertheless, it is in everyone’s best interest to find newer ways of ensuring workplace safety. It is in this context that IoT has emerged as a veritable beacon of light. Today, the general view taken on health and safety of workers is very different to what it was say in the days of Andrew Carnegie.
Back then, the general consensus seemed to be that a few lives were bound to be lost in the pursuit of wealth creation and that there was nothing an employer could do about it - if you died working a dangerous job, well, that was just your lot in life.
Today though, thankfully, we have come a long way from that sort of mindset. Today, there is an enormous societal emphasis being placed on worker rights. Companies face tremendous amounts of pressure in today’s information-savvy, internet-connected world. One bad move - one piece of news about a worker death - and boom! You are in the middle of a massive PR scandal.
This being the case, companies are sitting up and taking worker safety very seriously indeed. An increasing number of them are adopting very sophisticated IoT based technology to ensure workplace safety. Granted, these IoT-based worker safety systems do spell an increased investment, to begin with, more and more companies are taking the plunge. In the long term, they believe, it will be an investment that will more than pay for itself, in terms of money saved on expensive lawsuits, worker compensations and lost productivity.
Workplace mishaps come in all manner of forms - from chemical burns, heat strokes and equipment failures to lone workers being stranded in remote locations. Nearly every industry and occupation comes with its own long list of occupational hazards. Today, IoT offers us a way to limit these dangers and adopt best practices to make sure employees aren’t subject to anything more than the least amount of risk, while on the job.
Workplace safety is not just about saving lives or money. Although these are very compelling incentives in and of themselves, they add up to something more than just the sum of their parts, all said. When we find a way to eliminate the risk of human injury and death in a workplace, we actually end up accomplishing a whole lot more.
Safety in the workplace is about more than just the sum of its parts. Here’s a story that highlights just that.
In his bestselling book, The Power of Habit, Charles Duhigg narrates the story of Paul O’Neill, which we’ll take a brief look at here.
The incident pertains to a large American conglomerate called Aluminium Company of America - or Alcoa for short. A proper big-league corporation, Alcoa was, simply put, the one-stop-shop for everything aluminium related, supplying nearly every need for the metal from chocolate wraps and coke cans to the nuts and bolts of NASA satellites.
In the mid-1980s however, Alcoa which had been a reliable bet for investors thus far started flailing a bit. The investors started panicking as the management made blunder after blunder. Competitors were beginning to eat into Alcoa’s profits, as the company started making unwise moves to expand into new areas.
In a bid to put an end to this seeming decline, Alcoa’s board announced that it’d had enough and that new leadership was going to be put in place. A former high-ranking bureaucrat named Paul O’Neill was chosen for the job. This man was a relatively unknown entity in the world of Wall Street. Unsurprisingly, when the company scheduled a formal event in New York to unveil their new CEO, nearly every major investor made sure they were in attendance.
Cut to the moment where the new CEO takes the stage - he starts his much awaited address with the words, “I want to talk to you about worker safety. Every year, numerous Alcoa workers are injured so badly that they miss a day of work. Our safety record is better than the general American workforce, especially considering that our employees work with metals that are 1500 degrees and machines that can rip a man’s arm off. But that’s not good enough. I intend to make Alcoa the safest company in America. I intend to go for zero injuries”
Workplace safety seemed to be a rather bizarre choice of topic for an opening address by a new CEO. The big-league investors who were used to more run-of-the-mill CEO speeches were shocked. They stampeded out of the room and desperately tried to make calls to warn their clients against holding on to Alcoa stock.
“They’ve put a hippie in charge. He’s going to kill the company. Sell all your stock immediately”, one of the investors claims to have told one of his clients, immediately after the event. It would turn out to be, by his own admission, the worst piece of advice he’d ever given.
Cut to one year after O’Neill delivered that speech - Alcoa’s profits had hit a record high. By the time the man retired in 2000, the company’s annual income was 5 times what it had been before he’d arrived. Its market cap had gone up by a staggering $27 billion!
Before O’Neill took over Alcoa, every single Alcoa facility would have at least one mishap per week. Once his plan was implemented, most of these facilities wouldn’t have accidents for years.
How did this happen? And more importantly, what does it mean?
O’Neill saw safety as a central metric to assess how the habits of his company were changing, from the ground up. He wanted to create a culture of excellence, commitment and total ownership. He understood that he wouldn’t be able to do that with mere words. He needed to present an idea that everyone could get behind - an idea that would ripple outwards and end up creating a culture of excellence.
There are two salient points that we can take away from this story - if it is indeed faulty habits, flawed methodologies and apathy that have resulted in undesirable outcomes at the workplace, then that means that we can turn it around. That simply means that we haven’t done all that we can in ensuring the safety of workers.
But this also means that it isn’t a herculean task by any means to achieve remarkable results in terms of workplace safety. After all, O’Brien didn’t have access to the sort of data and technology that we do today. If we was able to make such an incredible change over such a short time, it really should give us hope in terms of what we can achieve using state-of-the-art IoT technology.
In the sections below, we’ll take a look at some of the ways in which IoT can help drive higher standards of safety in the workplace.
Driving safety through a connected workplace
We live in a hyper-connected age. Chances are when you hear the term “industrial internet of things”, you think of an entirely robot-powered assembly line putting decent, hard-working people out of work. In fact, however, many of these intelligent IIOT systems are actually seriously empowering worker safety - they’re actually helping us make our workplaces safer and healthier places to be in.
IoT systems are getting more ubiquitous by the day. There is not a single industry in the world that has been left untouched by the new technological revolution, that is the IoT. Manufacturing though seems to have forged a special and unbreakable bond with the internet of things. It is perhaps fair to say that no industry has been as receptive to the changes brought about by the IoT revolution, as the manufacturing industry.
It is a well-known fact that smart factories make for higher profits and productivity, driving greater efficiency and lower wastage. However, a lesser-known aspect of IIoT is how organisations are using it to build workplaces that are safer for their workers and to ensure greater health, well being and satisfaction among their workforce.
Technologies like wearable sensors, artificial intelligence and machine learning are helping us make massive strides in cutting down instances of injury and deaths in the workplace. These technologies are being leveraged in powerful ways to make workplaces more safe.
Speedy response during emergencies
Often it isn’t the nature of the accident itself that proves to be fatal or expensive but a delayed response to the accident. A speedy response can go a long way in limiting the damage and loss that a workplace accident causes.
So, how can IoT help in this kind of situation?
For instance, say a worker falls from a height or suddenly loses consciousness due to exhaustion, wireless sensors located at the site would trigger alarms that would ensure timely dispatch of medical help to the location of the accident.
This is probably the most simplified version of how IoT can help in an emergency situation. These systems can be extremely sophisticated and complex. Nevertheless, they follow a basic schema - IoT sensors pick up on some form of data which is crunched by an information processing unit and sent to a centralised server, where alerts are issued if patterns indicating some sort of danger to workers are observed.
Here’s an example of an IoT device that does just that - Blackline Safety’s G7 device is a jacket that is incorporated with wireless sensors. These smart sensors are able to detect the presence of harmful gases in a lone worker setting. It is chock full of relevant functionality such as fall detection, emergency latch, motion detection etc. Devices like these are an example of how modern IoT devices equipped with batteryless sensors can be invaluable in mitigating disaster in case of disastrous events.
On the job monitoring
Although advanced heavy machinery and robots shoulder a lot of the heavy lifting responsibilities in today’s industries, there are still many cases where human labour is used to lift and transport large objects.
This is especially the case in developing economies where labour is often incredibly cheap. Lifting these objects, especially when performed improperly, can be incredibly strenuous on the joints and can cause severe damage to one’s hips, lower back and arms.
In these situations, IoT wearables are able to monitor workers in real-time and identify the parts of the body that are going through the most strain at any given moment in time. Kinetic reflex is one such product that is targeted at reducing incidence of workplace injuries. This device is designed to be easily incorporated into a worker’s shirt or belt. This device is equipped with sensors which monitor the movements of workers as they are lifting weights and alert them when they get into high-risk positions.
Injury prevention is just one facet of what these technologies can do - they can also help in the creation of a robust data-set which can allow employers to analyse thousands and thousands of data points to come up with clear patterns which can be used to prevent further mishaps down the line.
Improving worker health and wellness
Accidents are one thing. Ensuring adequate worker wellness on a day to day basis is quite another. This is another key function that IoT can play in worker health and safety.
Data collected using IoT sensors can help identify the complex patterns that underlie occupational illnesses and health hazards. These systems can be used to create data-rich models which can help us design practices that promote employee well-being and in turn, productivity.
For instance, you can imagine a system where clever wireless sensors pick up data from the factory floor, such as temperature, humidity, CO2 levels, O2 levels, radiation, noise etc. These parameters are fed into a centralised system where a manager could look out for alarming signs and make timely calls to ask workers to take a much-needed break.
In doing so, these systems can actually cause the overall productivity of an organisation to skyrocket while also ensuring high employee morale. Systems like these can reduce the risk of chronic illness and stress among workers.
Predicting and preventing mishaps
Predictive analysis can help us create highly data-rich models that allow us to predict when an accident or injury is about to happen and prevent it.
How would this work?
Say, there are smart sensors deployed on bits of rock in a coal mine and measure seismic activity. These sensors have access to large troves of geological data that can be used to identify patterns that foretell the occurrence of a landslide. If the system picks up such a threat, early warnings can be given and a gruesome catastrophe can be prevented.
This is an example of a use-case where IoT really shines - a model based on collection, adaption and prediction - i.e building sophisticated datasets and using them to progressively build on existing models that get better and better over time at predicting when mishaps are about to happen.
This goes hand in hand with predictive maintenance systems that can predict equipment failures and maintenance jobs ahead of time, which allows for timely repairs to be done. Faulty equipment, more often than not, translates to higher chances of workplace mishaps.
Predictive maintenance systems are another great way of ensuring worker safety, in addition to adaptive learning systems.
Transport systems
Some industries more than others are especially vulnerable to the kinds of occupational hazards that we’ve been speaking about. The transport industry is one such example. For instance, Iot-based worker safety systems are indispensable in the trucking industry. Drivers and other fleet workers often spend most of their on-the-job time working alone. They are vulnerable to several types of risky situations. IoT based systems allow employers to take a measure of responsibility in ensuring the safety of drivers.
Real-time location tracking is the main priority with these solutions. Using IoT-based safety systems, employers are able to track the location of their drivers in real time, which can alert them in case of accidents or other such untoward events.
Lone Worker Safety Devices
Lone worker safety devices are a great example of IoT-based workplace safety solutions. As the name suggests, these are devices that are used in situations where individual employees perform work-related tasks in far flung, remote locations. These IoT devices are specifically designed to ensure the safety of employees and help them face unexpected challenges that they might encounter when they work alone.
So, what are some areas where these lone worker safety devices could be used?
These devices can be used pretty much in any situation where the employee works alone and the employer wants to ensure his safety on the job. Lone worker safety devices are increasingly also being used in more run of the mill situations like office work, when employees are required to be alone.
These days, employers are extremely concerned about the safety and wellbeing of their employees and are well aware of the huge ramifications that they could be subject to in case of a situation that challenges either. In the UK, for instance, recent statistics show an increase in the number of violence and grievous harm occurring at the workplace. Moreover, there is also a large number of injuries and accidents that happen at the workplace each year - in fact, they accounted for over 7% of all injuries last year - a risk that is especially high when it comes to people working by themselves.
In these types of situations, lone worker safety devices ensure that the employee can signal their distress and get help as soon as possible, reducing the chance of untoward delays that may prove costly, or even fatal.